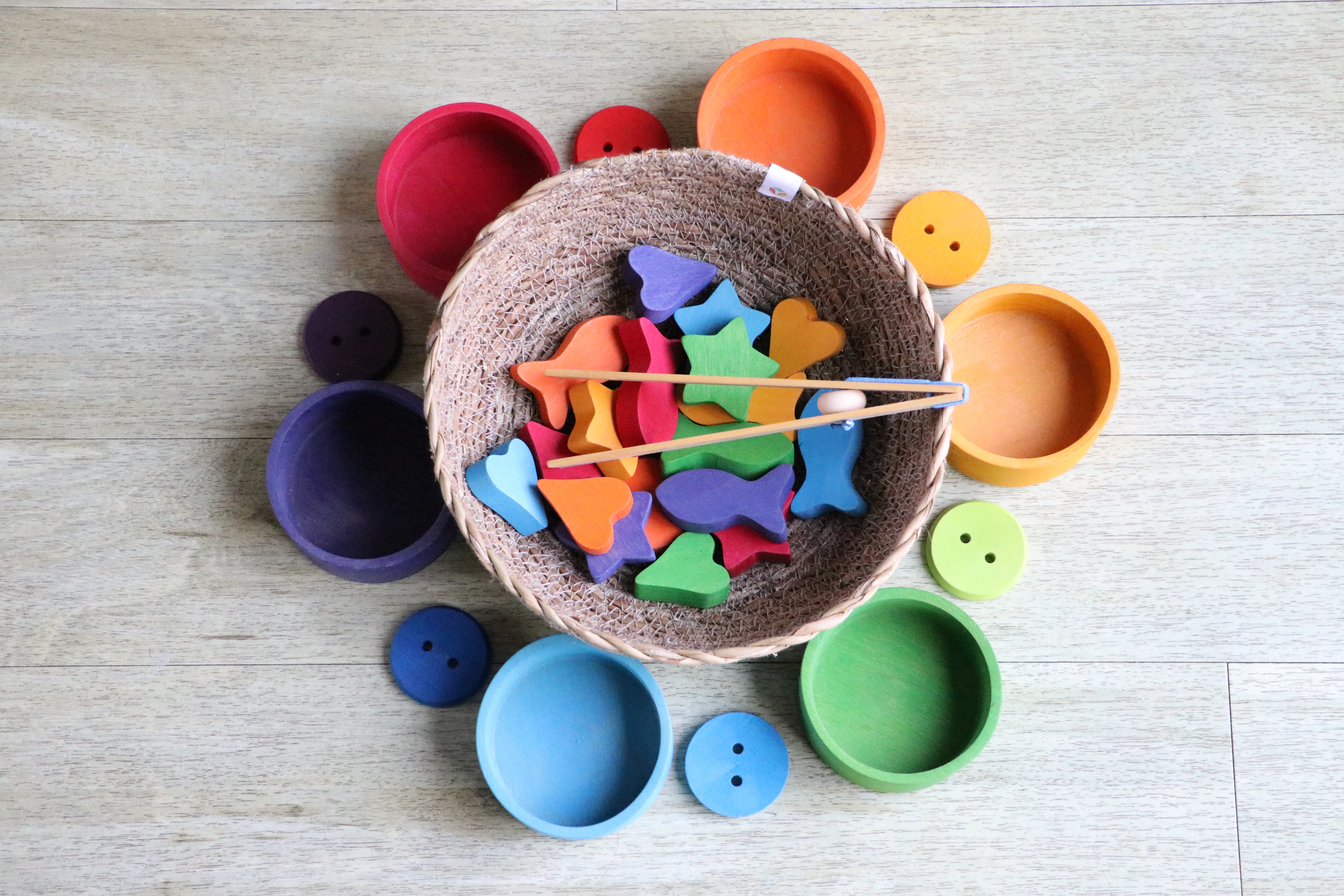
For many, using 5S is a natural method introducing lean. The threshold is low, and the results comes instantly. However, it is very common that organizations want to build a lean culture before introducing tools and methodologies, and this is actually where many fails.
Failure can be defined in many ways. Perhaps the goal and vision for the culture was set wrong. Perhaps the organization culture was already prepared to introduce lean?
Howcome?
Many aspects of lean and 5S is based on common sense. Basically, we are adding a language to what everyone is thinking – in this case Japanese terminology.
5S meaning - for the geeks
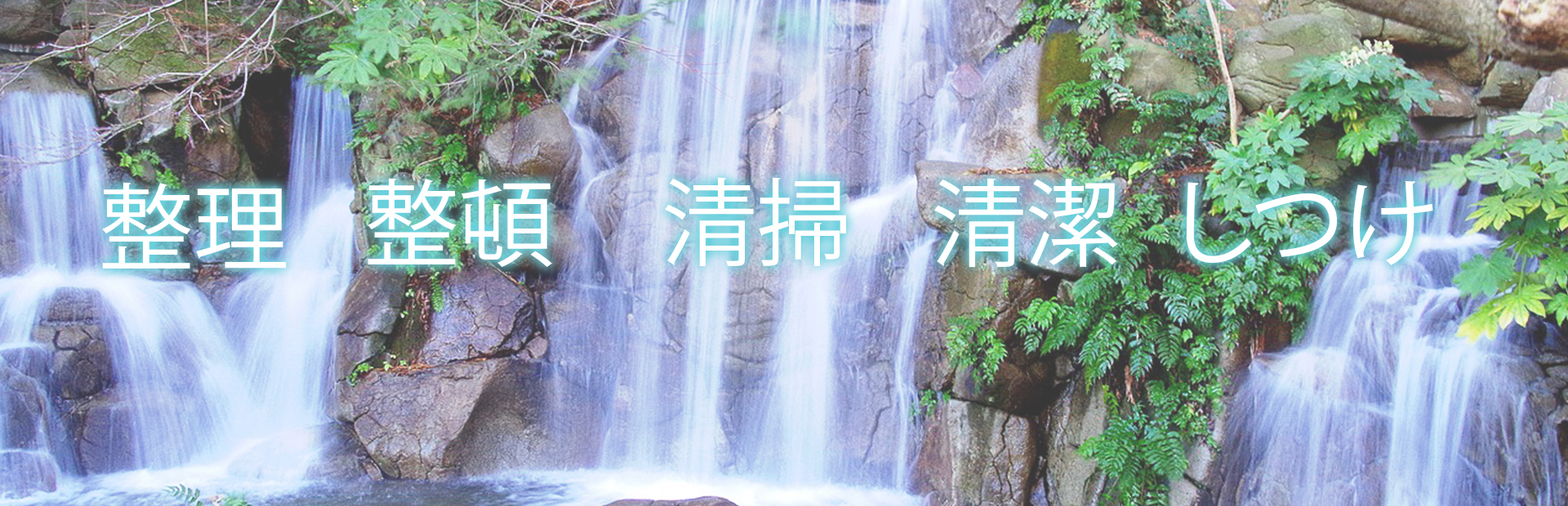
SEIRI
Meaning: Sorting
Remove items not relevant for the work or location.
- Reduce time looking for items.
- Reduce distraction due to mess
- Optimize use of space
SEITON
Meaning: Set in order, straighten
Create an optimal workflow by placing items where they are applicable. Keep tools and appliances near the task at hand.
SEISO
Meaning: Shine
Keep your workplace clean and tidy. Inspect and shine regularly to keep a pleasing workplace. Defects are detected more easily; waste and errors are reduced.
SEIKETSU
Meaning: Standardize
Ensure repetition of the first three S’s. This is where the practice is established supported by processes and procedures.
SHITSUKE
Meaning: Sustain self-discipline
When the practice is established, a culture is developed where people are self-motivated to continue and improve the new practice. The employees have taken ownership of the process.
Human psychology
Adding definitions and a language to intangible knowledge helps us focusing on the right things. It helps us communicate and thus improve and develop together.
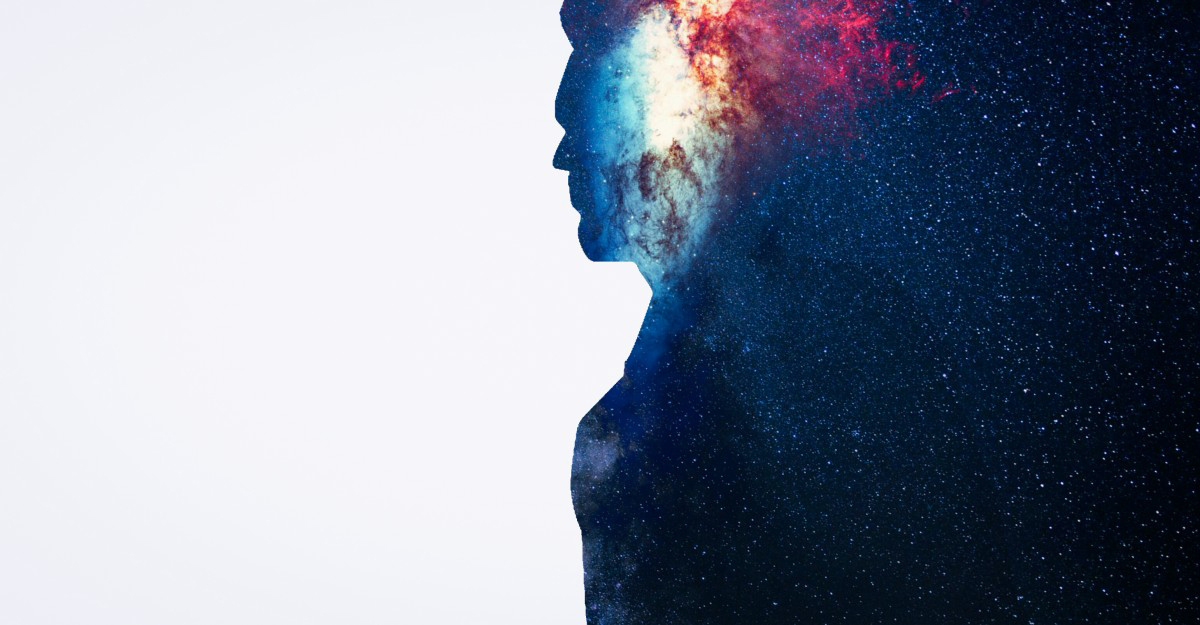
Mental coaches and various studies tell the same story about how we can be more satisfied in our personal life. The facets are pretty much the same as in lean 5S. Take this article from Forbes as an example: “Ten Hacks For Simplifying Your Life”.
- The two first points are about getting rid of unnecessary stuff (and people). This resembles the first S.
- The next is meal planning. This is the second S – keeping things available when needed, where needed.
- Fourth item “Create a morning ritual” is represents the fourth S – standardize with a certain process.
- And so on…
“Categorizing people is an easy and efficient way of simplifying the world and reducing mental effort.”
The book “Social Psychology and Human Nature” (R.F. Baumeister PhD, B.J. Bushman PH.D, 1980) elaborates on relations between people. There are many effects of human psychology in play here, and they can relate to lean. We use social categorization every day without thinking about it. A big difference between sorting people and objects is the level of emotional involvement. Despite this, sorting people is easy, but sorting items at your workplace often seems difficult. It is all about structure, practice and making a change – of course supported by the company’s management.
Practice only fails if you stop trying. If you keep failing, you need to change your approach.
“The definition of insanity is doing something over and over again and expecting a different result.” Albert Einstein
I do believe that we are all practicing 5S to some extent every day without using the definitions, and not sharing these thoughts with others. Except when calling it common sense. Perhaps our own mental barriers are preventing success. If we break down the walls, we can invite success.
If you want to know more or would like an online demonstration of DigiLEAN.tools, please contact us!